Office Building Expansion
The overall hi-rib steel exterior finish, vertical slider windows and paint colors complement the exterior of the warehouse located next to it. The building is being used by Upper Management so high end finishes were used. Luxury vinyl plank flooring, solid core wood doors, Commercial glass entrance doors and a glass interior wall were installed to provide a professional, upgraded look. Phone and data boxes were located to accommodate custom furniture installed at site. A receptionist window was installed to impede foot traffic through office by factory personnel.
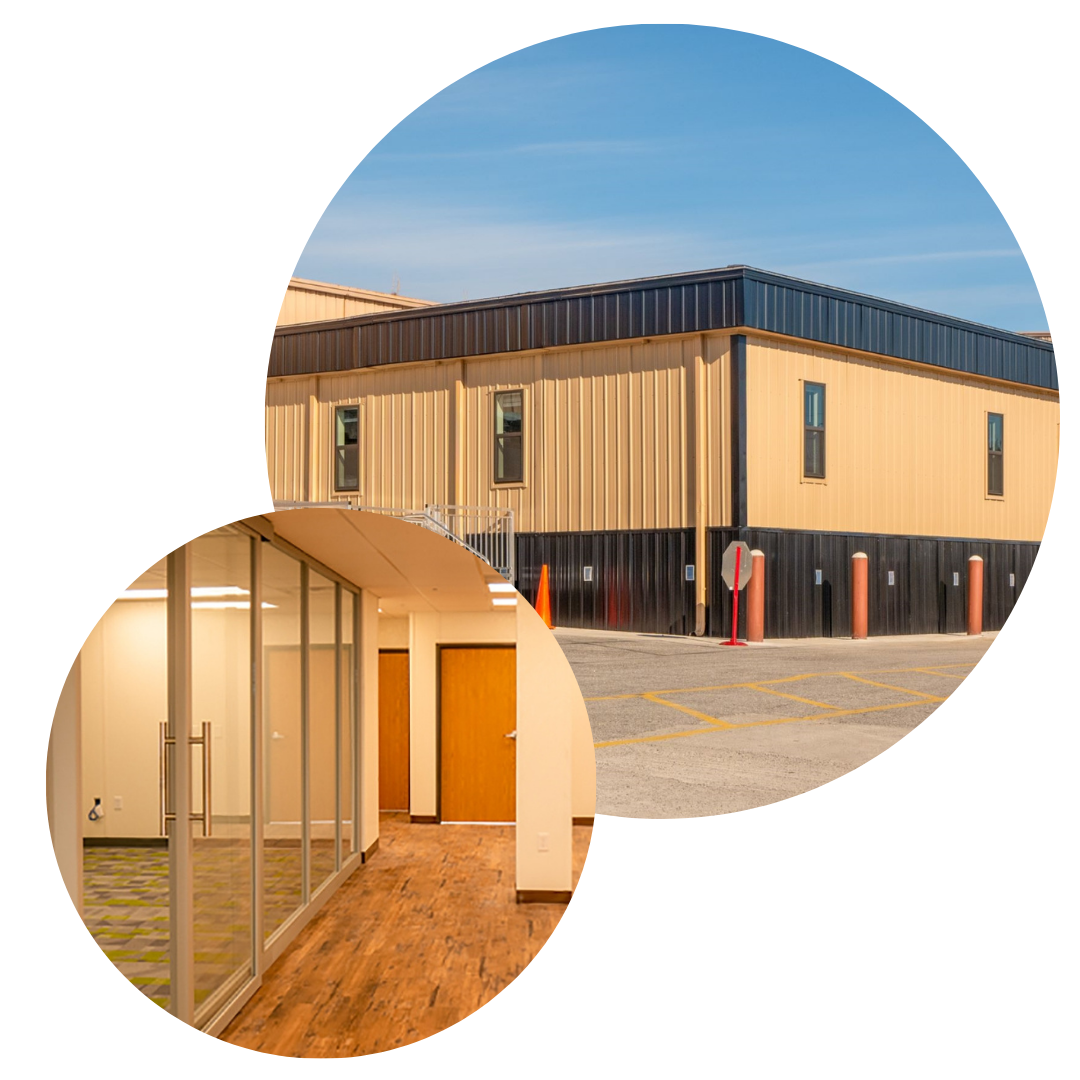
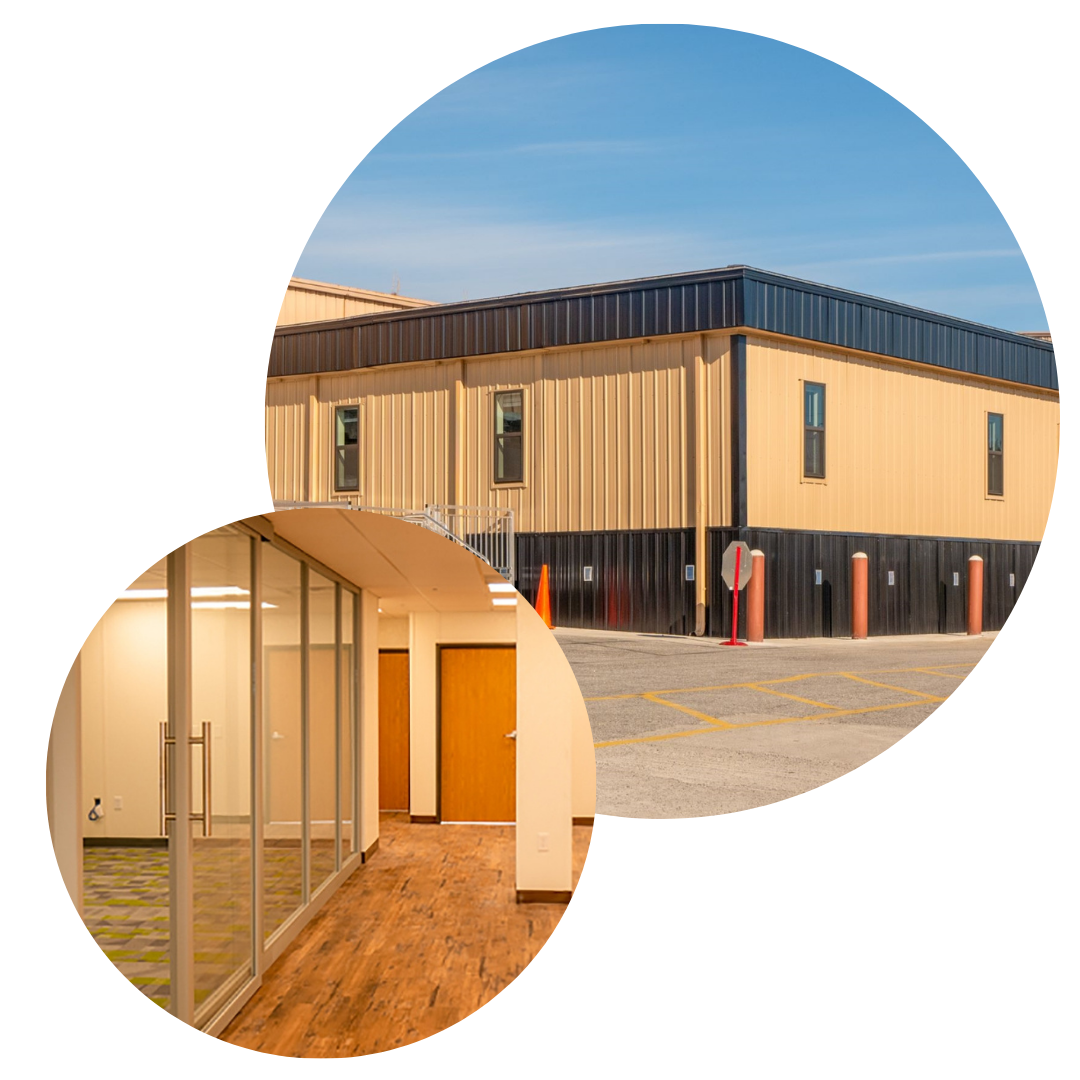
Office Building Expansion
The overall hi-rib steel exterior finish, vertical slider windows and paint colors complement the exterior of the warehouse located next to it. The building is being used by Upper Management so high end finishes were used. Luxury vinyl plank flooring, solid core wood doors, Commercial glass entrance doors and a glass interior wall were installed to provide a professional, upgraded look. Phone and data boxes were located to accommodate custom furniture installed at site. A receptionist window was installed to impede foot traffic through office by factory personnel.
Permanent Modular Office
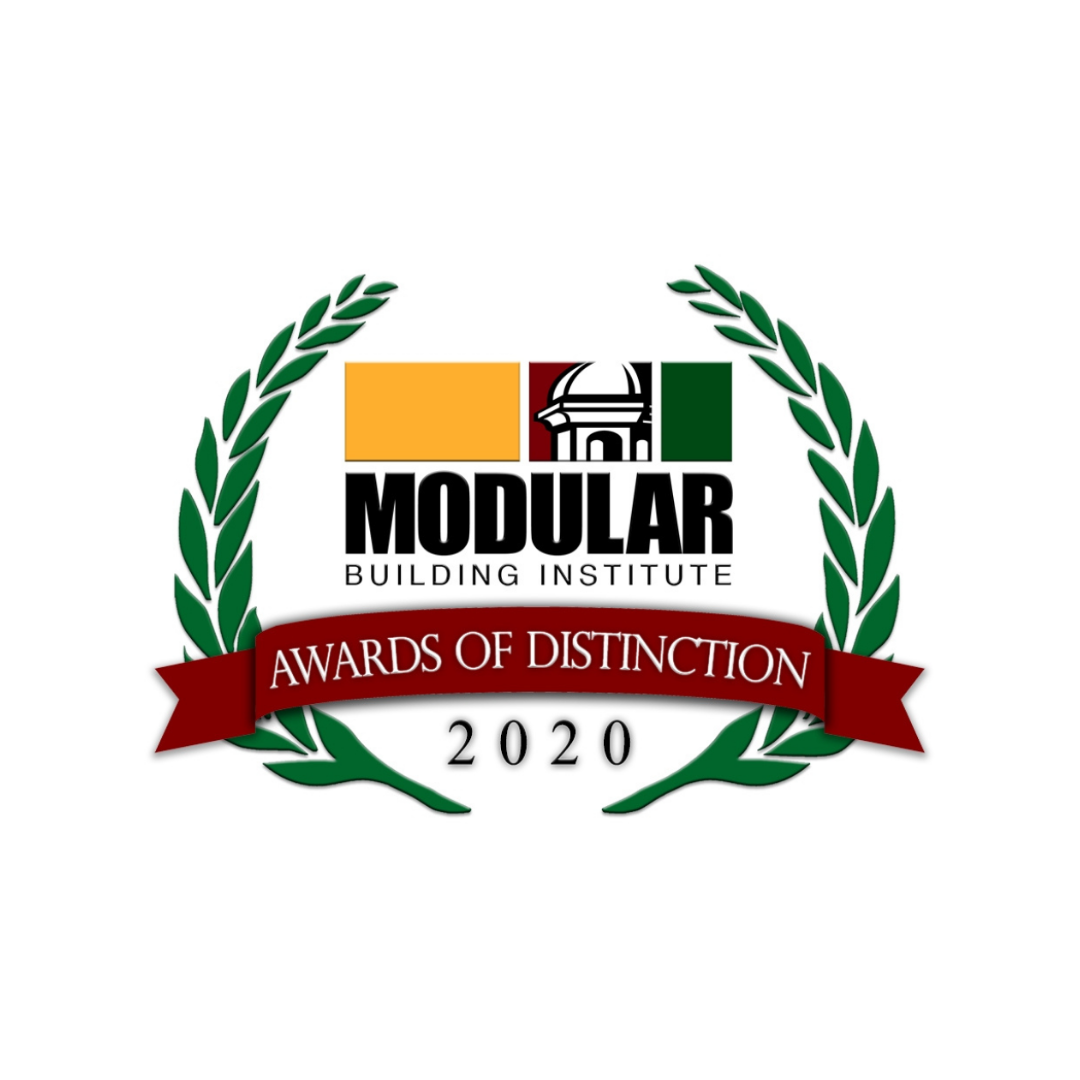
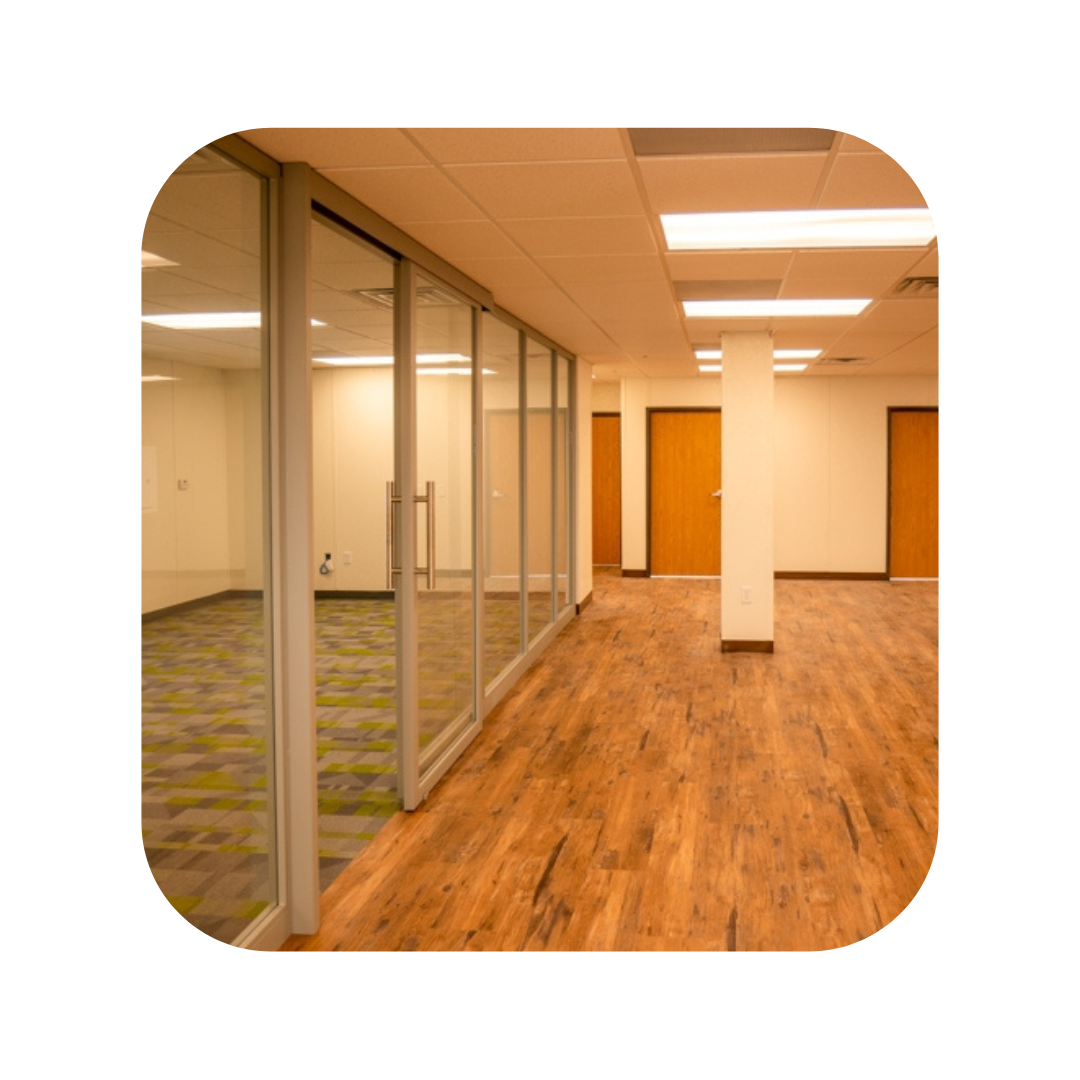
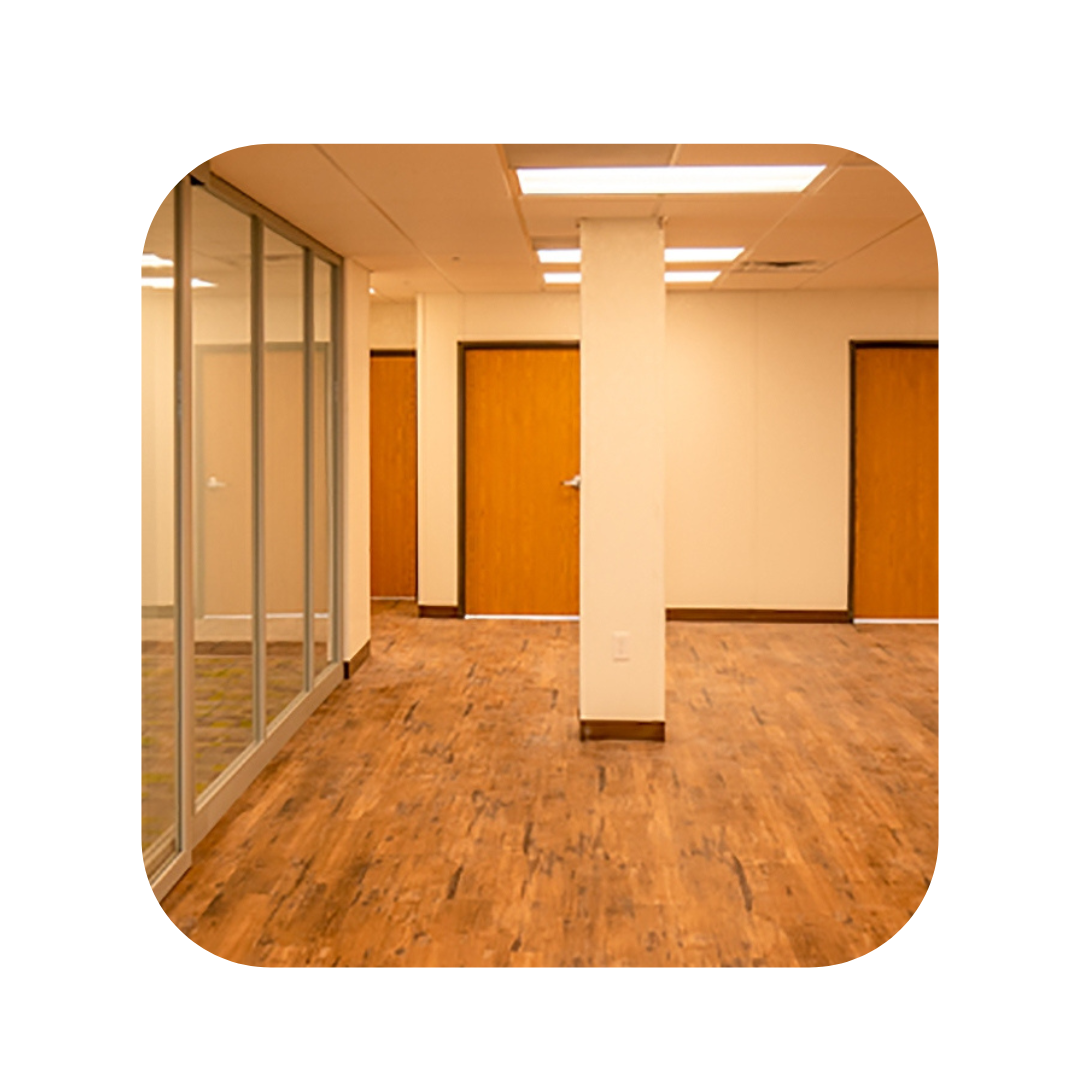
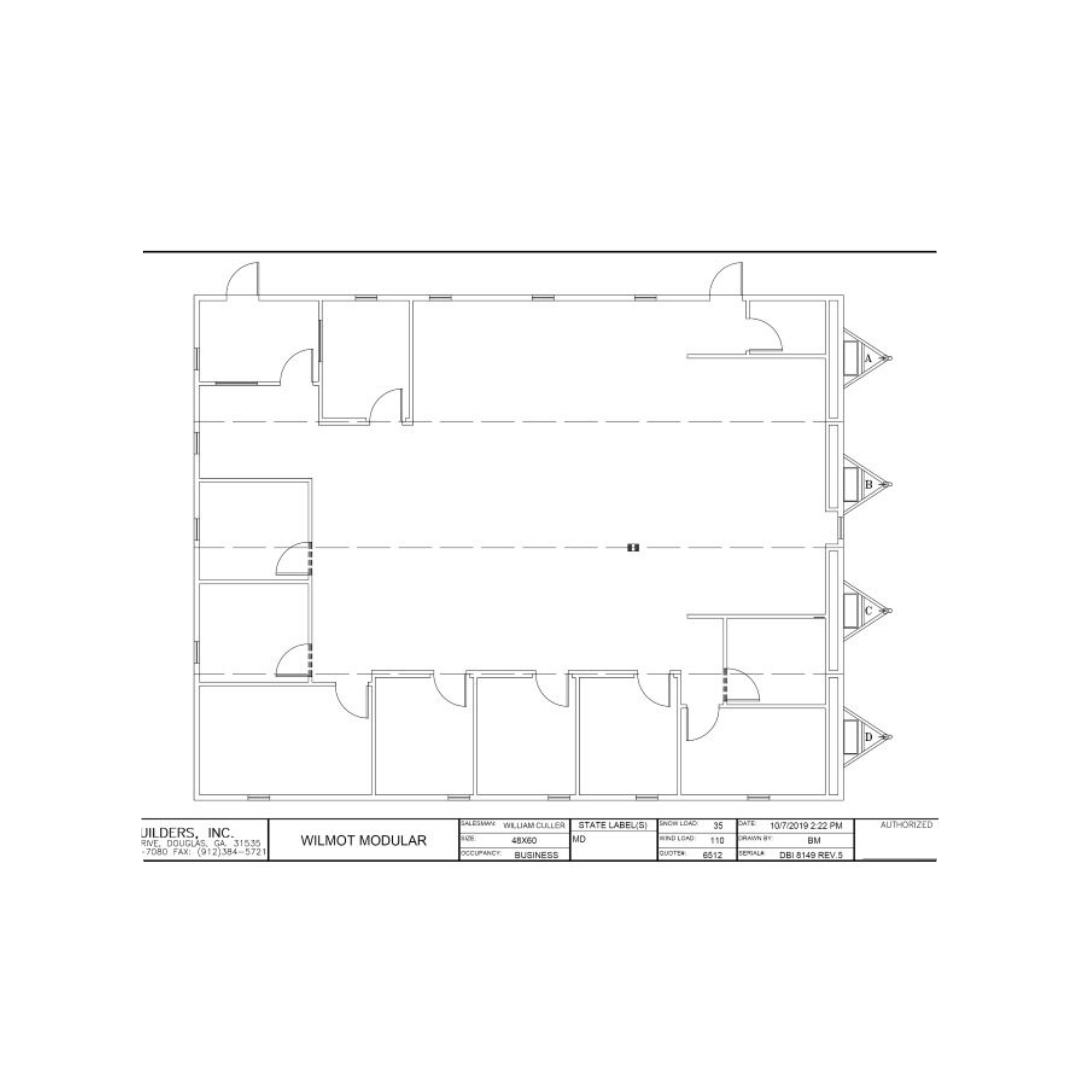
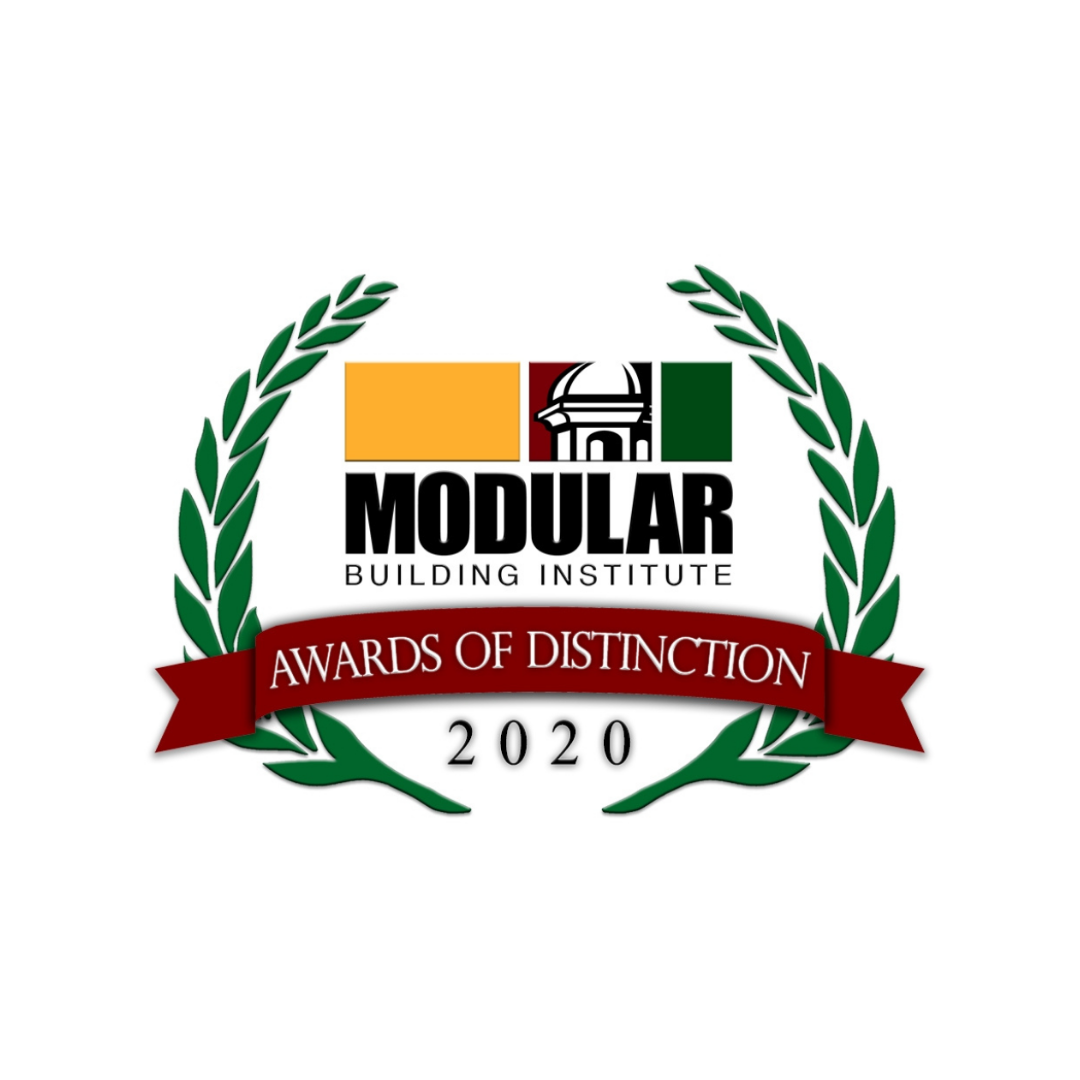
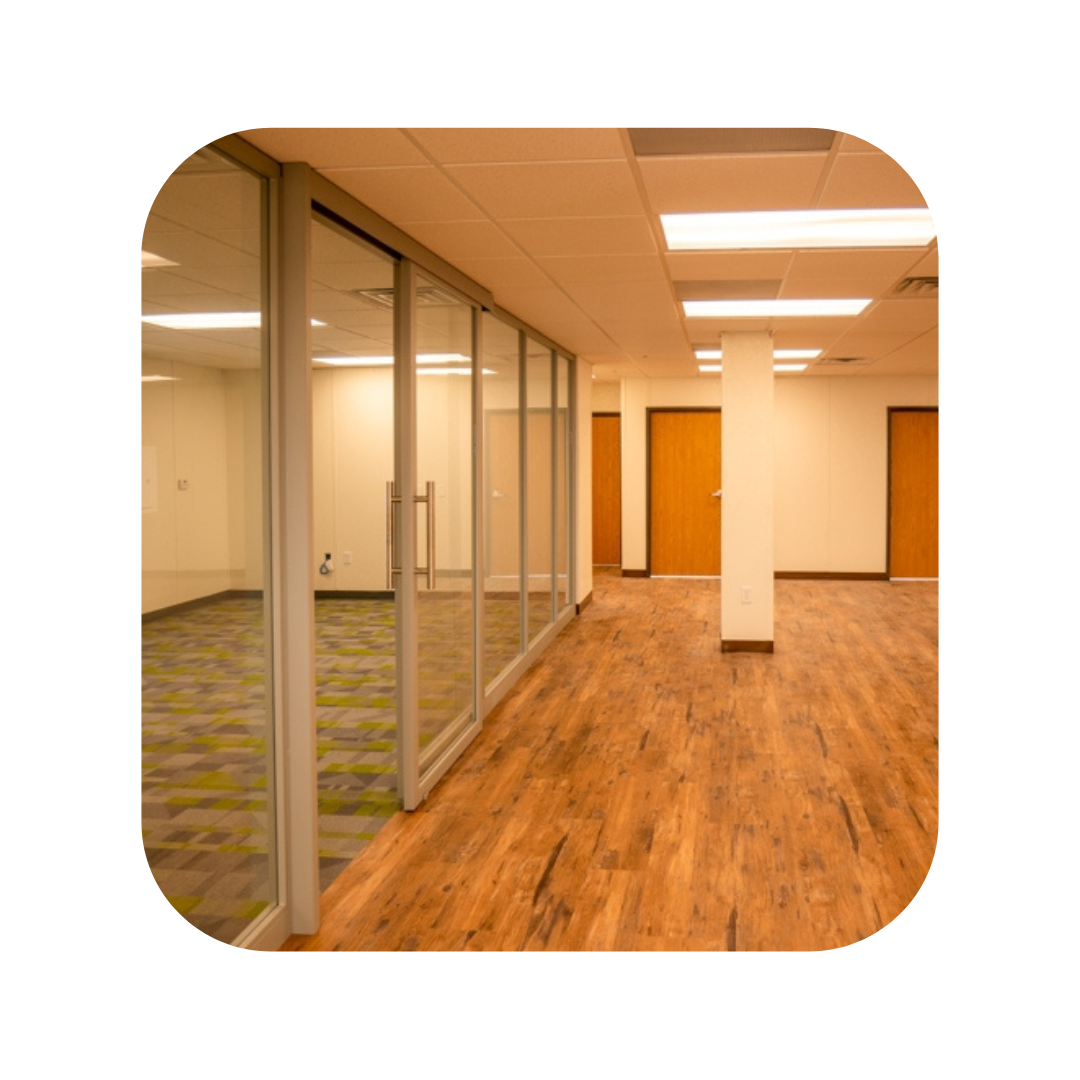
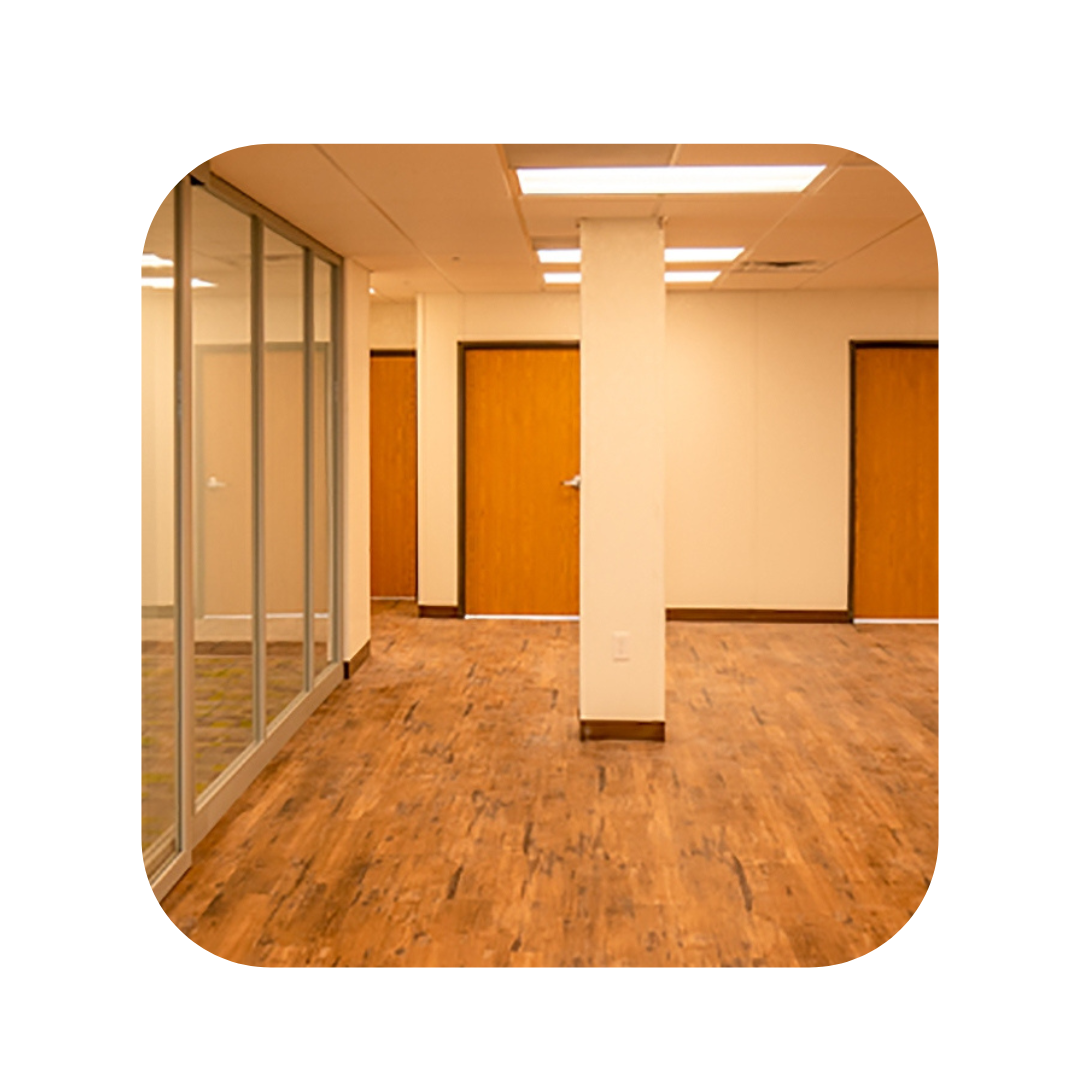
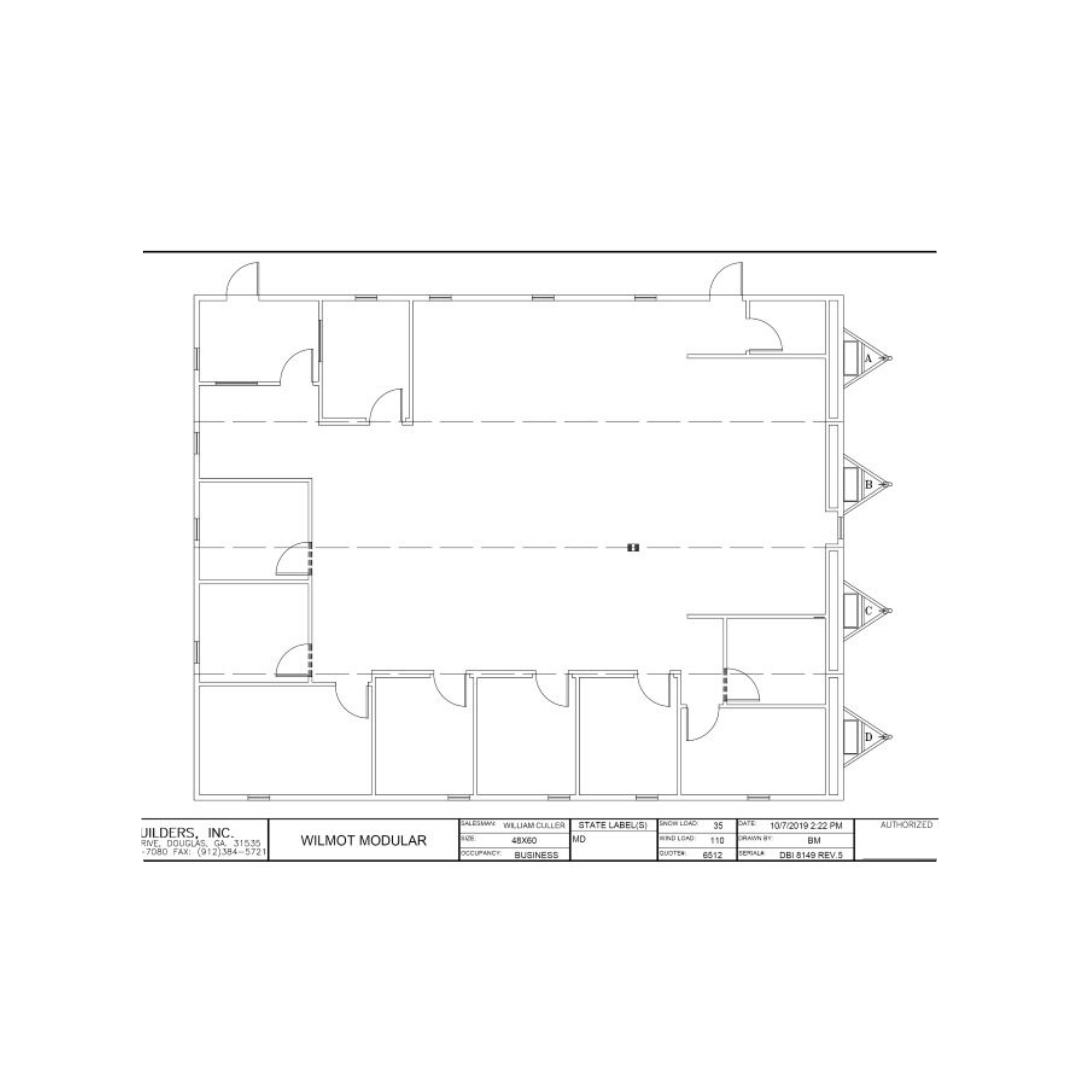
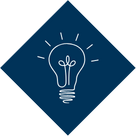
Technical Innovation & Sustainability
There were many challenges to this site including adherence to stringent safety requirements. An existing building was removed and this modular building was put in its place. Because the excavated site could not support the weight of the concrete truck, it had to be dug out and reinforced to enable ground stabilization.
A perimeter frame was used for durability and longevity. A tegular tile ceiling with LED lights was installed on site for energy efficiency. Because of the close proximity to the warehouse, Type X, fire rated gypsum was used with interior walls extended past ceiling to roof. That created an overheight building so underslung axles were installed to lower the shipping height.
Roughins for the sprinkler system were installed at factory with piping, riser and backflow done on site. Wallhung HVAC units were installed with a plenum wall to provide for sound attenuation.
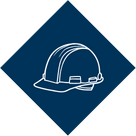
Cost Effectiveness
The customer chose to remove an existing modular building and replace with this new building on the same footprint to minimize permitting and local jurisdiction requirements for new buildings. Wilmot fabricated axles and hitches out of used equipment rather than selling new equipment in order to move the building off the site.
Modular construction was the biggest cost savings to Customer due to the stringent safety and site requirements. The time spent on site by contractors was less then ½ the time it would have taken with standard construction.
The cost for Special harnesses and cables, EMT and Rescue Team personnel needed while working in confined spaces, daily permitting requirements, extensive safety training for all laborers, ground penetrating radar used every 4’-7’ when soil was disturbed and the excavation and construction of retaining walls were all minimized by cutting down the time on site and the amount of soil disturbance.
Project Details:
Affiliate: Diamond Builder
Location: Baltimore, MD
Building Use: Office
Number of Modules: 4
Total Square Feet: 2880
Days to Complete: 176
Looking to learn more?
Contact Diamond Builders Today: